X-ray Inspection
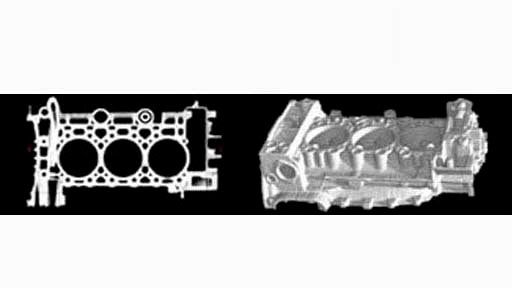
- Radiographic inspection for spot checks as well as for 100% inspection to find internal defects in safety and function-critical components and assemblies, geometric measurement of internal contours, avoidance of scrap refinement in expensive workpieces or in development
- Conventional X-ray inspection is based on two-dimensional images, computed tomography allows three-dimensional volume data sets to be obtained
- Typical applications are the inspection of castings for blowholes, inclusions and porosity or looseness
- User industries are automotive and automotive supplier industry, aerospace, metal and electrical industry as well as foundries
The X-ray or radiographic examination is a non-destructive method for two- and three-dimensional inspections of components for internal defects as well as for geometric testing. Radiographic inspections are implemented in order to identify internal defects in safety-critical and function-critical components and assemblies, to geometrically measure inner contours, to avoid reject part refining in expensive workpieces or in development. For this purpose, the test items are irradiated with high-energy electromagnetic radiation such as X-rays and gamma radiation. Inhomogeneities and defects in the entire cross-section of workpieces, made of materials of all kinds, lead to different weakening of the permeating radiation. Weakenings are in principle detected by a digital X-ray camera arranged behind the test object. The attenuation coefficient is highly dependent on the material density. Optionally, the workpiece is irradiated from several directions. Data is processed to a volume data set by means of a mathematical method which enables the production of sectional images and 3D views in arbitrary levels of the test object. Similarly, the testing of sealed and poured in modules on assembly errors or completeness is possible. The two-dimensional images are processed by an image processing system and evaluated visually or automatically. Typical applications include the inspection of casting parts for shrink holes, inclusions and porosity or loosening. Steering knuckle, rear axle trailing arms, suspension strut cover, airbag capsules, brakes, alloy wheels or tires as well as general welds can be checked. Other applications include geometric measurements of the inner contours, such as cooling channels in cylinder heads. A testing device typically includes a radiation shield, a manipulator for handling the workpieces or the beam source and detectors, a beam source, and a digital x-ray camera. The evaluation is performed visually or by an automatic image processing system. The user industries include the automotive and automotive supply industries, the aerospace industry, the metal and electrical industries and foundries.
Suppliers: X-ray Inspection
Baker Hughes, a GE company LLC | |
Balteau NDT S.A., Hermalle-sous-argenteau, Belgien | |
Bosello High Technology S.r.L., Cassano Magnago (VA), Italien | |
GE Inspection Technologies, Huerth, Deutschland | |
Gilardoni S.p.A., Mandello del Lario Lecco, Italien | |
MatriX Technologies GmbH, Neubiberg, Deutschland | |
ProCon X-Ray GmbH, Sarstedt, Deutschland | |
YXLON International GmbH, Hamburg, Deutschland |