Eddy Current Testing
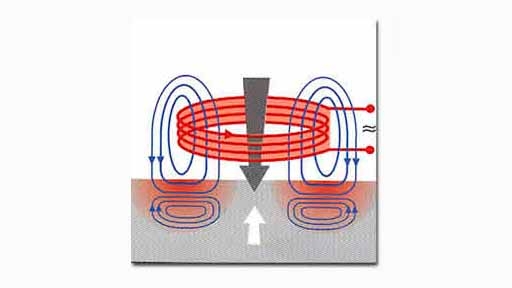
- Eddy current testing is used to detect defects that are open or close to the surface, such as cracks or pores; the detection of microstructural defects is also possible
- High testing speeds and the possibility of testing electrically or magnetically conductive components even in very large quantities
- 100% inspection of safety and function-critical machined components as well as semi-finished products for the manufacture of these components
- Typical test specimens are components and small parts with flat or rotationally symmetrical test surfaces such as cylinder running surfaces, hardened or ground surfaces e.g. on bearing seats of crankshafts, camshafts, the cams of camshafts or valve seats
- Small bulk parts or rod-shaped products such as racks, tubes or wire are also inspected
- User industries include the automotive and automotive supplier industry, manufacturers and processors of semi-finished products, pipes and wires made of metal, mechanical engineering, etc.
The eddy current test is a non-destructive test method for the detection of surface-open cracks and pores, near-surface defects on electrically or magnetically conductive surfaces as well as microstructural defects. The method offers high test speeds and is suitable for testing electrically or magnetically conductive components even in very large quantities. It is used for 100% control of safety and functional critical machined components as well as semi-finished products for the production of these components. For testing, the surface is scanned with a non-contact or contacting probe which generates magnetic fields through an AC current coil in order to generate eddy currents on the surface of the device to be tested. These eddy currents in turn generate electromagnetic fields, which are detected by the receiving part of the test probe. In principle, the probes only recognize cracks which run transversely to the direction of the probe movement. Therefore, it is necessary to perform the scanning movement in different directions. A flat surface is scanned with flat rotors. The testing of rod-shaped components is realized by coils for detecting transverse cracks and rotating heads, which rotate about the longitudinal axis of the test item while it is continuously advanced. Conversely, rotationally symmetric outer and inner surfaces can be scanned by a stationary probe by rotating the component. The inspection of complex shaped parts such as turbine blades may require robotic handling. Typical test items are components and small parts with flat or rotationally symmetrical test surfaces such as cylinder surfaces, hardened or polished surfaces on plummer blocks of crankshafts, camshafts, the cam lobes of camshaft or valve seats. Also small bulk goods or rod-shaped products such as racks, pipes or wire are tested. User industries include the automotive and automotive supply industries, manufacturers and processors of semi-finished products, pipes and wires made of metal, mechanical engineering.
Products: Eddy Current Testing
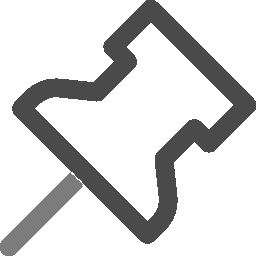
Suppliers: Eddy Current Testing
GE Inspection Technologies, Huerth, Deutschland | |
Institut Dr. Foerster GmbH & Co. KG - Division Komponentenprüfung CT, Reutlingen, Deutschland | |
KARL DEUTSCH Prüf- und Messgerätebau GmbH & Co. KG, Wuppertal, Deutschland | |
LAW-NDT Mess- und Prüfsysteme Vertriebs GmbH, Burgschwalbach, Deutschland | |
MARPOSS GmbH, Weinstadt, Deutschland | |
PRÜFTECHNIK Dieter Busch GmbH | |
Quality Material Inspection, Inc | |
Rohmann GmbH, Frankenthal, Deutschland | |
TMT Test Maschinen Technik, Schwarmstedt, Deutschland | |
Verimation Technology, Inc. |