Noise Analysis for Function Testing
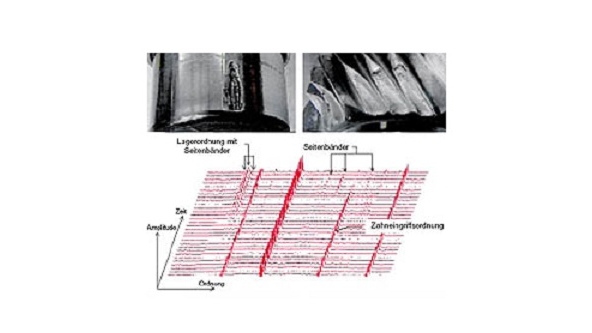
- Used as an automated noise analysis for end-of-line function testing of driven assemblies and systems
- Assembly inspection of assembled gears and toothings
- Another area of application is endurance test benches for early damage detection in the laboratory and development areas
- Typical areas of application: Testing of automatic, manual, transfer and axle gearboxes, hot and cold testing of combustion engines, electric motors with and without gears, adjustment systems, electrical devices and loudspeakers
Noise analysis for mechanical function testing is a test method in which assemblies and systems are checked in operation with the aid of their vibration behaviour or noise development by recording structure-borne or airborne sound. The test object is driven by its own or an external drive in no-load operation or under load and the resulting structure-borne or airborne sound is recorded. Mechanical faults such as machining faults or dents in gears, imbalances, bearing damage, grinding and other deviations cause a change in the vibration behaviour or sound signature compared to the sound signature of fault-free test specimens, which serve as a reference. Within the scope of the assembly check, the completeness of all assembled parts, the installation position or the part fit can be checked. In the function test, the mechanical function of assemblies can be summarily evaluated or the function of electro-acoustic transducers can be tested. The evaluation unit compares the measured values with the target values and thus detects acoustically conspicuous and defective test items.
A test station always comprises a component-specific workpiece fixture and, if necessary, a drive, contact or non-contact vibration sensors or even microphones as well as measurement and evaluation electronics with software.
The test system is set up by learning the sound signatures of a series of defect-free products that serve as a reference. The measurement is based on structure-borne sound analysis, which can be performed with different vibration detection systems. Either an acceleration sensor is mounted as a vibration transducer, e.g. on the workpiece, in the component-specific workpiece fixture or on the clamping plate. If non-contact vibration recording is required, laser or ultrasonic vibrometers or microphones can be used. When recording airborne sound with a microphone in the production environment, it may be necessary to filter out and suppress disturbing background noise.
The measured vibration curve is compared with the taught-in sound pattern, allowing changes to be detected. Deviations outside the specified tolerances allow damage to be detected.
Suppliers: Noise Analysis for Function Testing
Brüel & Kjaer Sound & Vibration Measurement A/S, Naerum, Denmark |
Discom GmbH, Göttingen, Germany |
Polytec GmbH, Waldbronn, Germany |
Reilhofer KG, Karlsfeld, Germany |
RTE Akustik + Prüftechnik GmbH, Pfinztal/ Karlsruhe, Germany |
SCHUNK Electronic Solutions GmbH, St. Georgen, Germany |