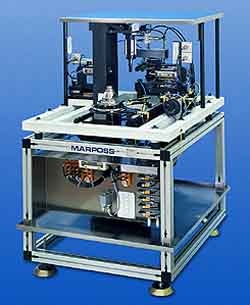
- Vollautomatische kundenspezifische dimensionelle Mehrstellenmesseinrichtungen
- Aufbau im Baukastensystem mit bewährten Komponenten
- Anwendungsspezifisch taktile Messtechnik
- Messtaster: z. B. induktive HBT- und LVDT-Messtaster, digitale Längenmesstaster Digi Crown™, inkrementale Längenmesstaster
- Automatische Verkettung und Handhabung z. B. mit Roboter oder Portalachsen
- Leistungsfähige Messrechner und Software
- SPC-Datenauswertung und Visualisierung nach Q-DAS-Norm, nationalen und internationalen Festlegungen (DIN, ISO) sowie nach Anwenderrichtlinien
Die vollautomatischen Post-Prozess Mehrstellen Messeinrichtungen von Marposs dienen für statische und dynamische Mehrstellenmessaufgaben zur Geometrieprüfung und statistischen Prozesssteuerung (SPC, Statistical Process Control). Die Messeinrichtungen werden im Baukastenprinzip als kundenspezifische Lösungen realisiert und in die Fertigungslinie integriert. Die Geometrie des Werkstücks wird in einem Messzyklus synchron mit einer Vielzahl von Messwertaufnehmern erfasst. Zur Messwerterfassung dienen berührende Messtaster wie z. B. induktive HBT- und LVDT-Messtaster, digitale Längenmesstaster Digi Crown™ und inkrementale Längenmesstaster. Für eine automatische oder manuelle Werkzeugkorrektur wird im Messrechner die Messwerterfassung, -verarbeitung und statistische Auswertung bzw. Analyse und Datenspeicherung durchgeführt.
Das Werkstück wird automatisch zugeführt und von einem Roboter oder mit Portalachsen in eine Werkstückhalterung in der Messstation gesetzt und fixiert. Wellen- und nabenförmigen Werkstücke werden entweder stehend oder liegend eingespannt und während der Messung in Umfangsrichtung gedreht. Bei den Messungen werden die Messtaster mit pneumatischen oder elektrischen Betätigungen gegen das Werkstück gefahren und die vorgegebenen Messpunkte angetastet. Wellen- und nabenförmige Bauteile können während der Messung rotieren oder sie werden in vorprogrammierten Positionen gestoppt und vermessen. Die Messwerte werden von einem Messrechner erfasst, ausgewertet, visualisiert und in den gewünschten Datenformaten abgespeichert.
Beim Einsatz als Post-Prozess-Messeinrichtung ist die Messstation entweder unmittelbar in die Bearbeitungsstation integriert oder als separate Messstation einer Prozess- und Bearbeitungsstation nachgeordnet. Bei jedem Fertigungsschritt kann die Produktqualität durch systematische oder zufällige Fehler beeinträchtigt werden, die an verschiedenen Stellen zu Abweichungen der Bauteilgeometrie führt. Hierbei kann es sich um zufällige Fehler wie z. B. Maschinenschwingungen handeln, die durch die Herstellung selbst bestimmt und kaum korrigierbar sind.
Im Gegensatz dazu können systematische Abweichungen z. B. durch Werkzeugverschleiß, Temperaturänderungen, Spannfehler der Bearbeitungsmaschine oder Werkzeugbruch mit Hilfe einer regelmäßigen Messung an einer Vielzahl von Punkten erkannt werden. Durch Auswertung und Speicherung einer Vielzahl von Daten lassen sich solche systematische Abweichungen lokalisieren und durch geeignete Korrekturmaßnahmen reduzieren oder völlig beheben.
Die aufgabenspezifischen Messeinrichtungen werden als schlüsselfertige Lösung realisiert und umfassen den maschinentechnischen Aufbau, die komplette anwendungsspezifische Messtechnik mit Messtastern und Sensoren sowie die Messelektronik mit Software, was soweit wie möglich mit bewährten Standardkomponenten von Marposs realisiert wird. Dazu kommen alle erforderlichen Verkettungs- und Handhabungsvorrichtungen sowie die Integration in die Fertigungslinie. Auch Teillösungen sind möglich.
Die vollautomatischen Post-Prozess-Messeinrichtungen werden für dimensionelle und geometrische Mehrstellenmessaufgaben mit einer Vielzahl von Messstellen eingesetzt und dienen zur Geometrieprüfung und statistischen Prozesssteuerung (SPC). Es können statische und dynamische Messzyklen mit einer unbegrenzten Anzahl von Messschritten realisiert werden. Typische Einsatzbereiche sind Messungen unmittelbar nach dem Bearbeitungsprozess zur automatischen Korrektur der Bearbeitungswerkzeuge, der Maschine oder des Prozesses in größeren Stückzahlen. Möglich sind sowohl Stichproben oder eine 100-%-Kontrolle. In der Regel werden eng tolerierte komplexe Bauteile mit wellenförmiger, nabenförmiger oder kubischer Geometrie geprüft wie z. B. Kurbelwellen, Radnaben, Zylinderköpfe oder Getriebegehäuse. Typischere Anwenderbranchen sind die Automobilzuliefer- und die Automobilindustrie.